Faux Fur: A Fact File
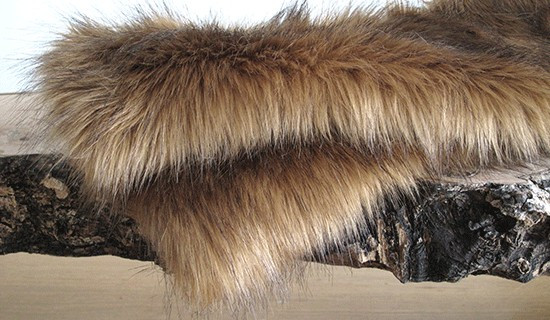
A brief lesson in fake fur; or 'Faux Fur: A Fact File', and that's a lot of F's!
Origins of the word
The word “faux” originally comes from the French word “faux” meaning “false”. It has been used in the English language at least since 1676 as part of a double-barrel word such as “faux-prude”. The word has only been used by itself to mean “fake” (with its French pronunciation) since the 1980s.
A history of faux fur
Faux fur was developed in 1929 but was not made commercially available until the 1950s. Despite its desirability, real fur was considered highly expensive and was hard to come across. Since then, faux fur has increased in popularity due to its promotion by animal rights and animal welfare organisations as a humane alternative to real fur home furnishings and clothing.
Fake fur was initially made using hair from alpacas, but was poorly made and therefore difficult to use in fashion and home design. Manufacturers continued to improve the quality of their faux fur by increasing its resistance and experimenting with more desirable colours.
What is faux fur made of?
The bulk fibres in fake fur are typically composed of polymers including acrylics and modacrylics. Acrylic polymers are sourced from chemicals derived from coal, air, water, petroleum and limestone. Secondary monomers are also added to allow the fibres to absorb coloured dyes for aesthetic purposes. Naturally occurring fabrics such as silk, wool and mohair can sometimes be used to improve the overall quality of the fabric.
How is it made?
Due to advancements in technology, the creation of faux fur is now a predominantly automated process made up of 3 main steps:
Step 1: Production of synthetic fibres
- Acrylonitrile and vinyl chloride monomers are mixed in a large steel container. They are then placed in a chamber where high pressure and temperature combined with mixing places polymerizes them. A white powdery resin is produced which is then dissolved in acetone.
- The polymer mixture is pumped through a filter, then through spinnerets until they are submerged in water. When the polymer is extruded through, it becomes a group of fibres called a tow.
- The tow is pulled along a conveyor belt and then stretched, washed and dried. Once the fibres are strong enough, they are sent to a machine and cut into appropriate sizes.
- The fibres then go through various quality control checks and are then soaked in dye solutions to change their background colour.
Step 2: Production of fur
- Taking into consideration the purpose of the fur, the backing is then sent through a machine to be cut into shape before the fibres are attached.
- There are now several ways of converting the fibres into a garment. The most common is the weaving process. Here, fibres are interwoven with the backing fabric.
- Another option is tufting. This way, garments are produced at a much higher rate. Circular loop knitting and sliver knitting are the other methods for fake fur production, and probably the most popular.
Step 3: Aesthetic touches
- In order for the garments to look like natural fur, they must be treated. First, the fabric is treated to ensure the colour does not fade. Wire brushes are then passed through the fabric to remove loose fibres. The fibres are then cut to an equal length and polished.
- Chemicals such as resins and silicones are then applied to improve the fabric’s look and feel. The fabric is then coloured to imitate real fur patterns. If fur is to be curled, the fabric is now embossed.
- The fake fur is then labelled as imitation fur fabrics before being packaged and shipped to the distributor.
What is faux fur used for?
Faux fur is most commonly known for its use in fashion. However, it is also used to make a variety of home decorations, including pillows, bedding and throws. The use of a faux fur throw in decorating schemes has become increasingly popular in recent years due to their authentic look and feel, and the variety of patterns, hair length and colours now available.
Comments
No comment at this time!
Leave your comment